MOTOR
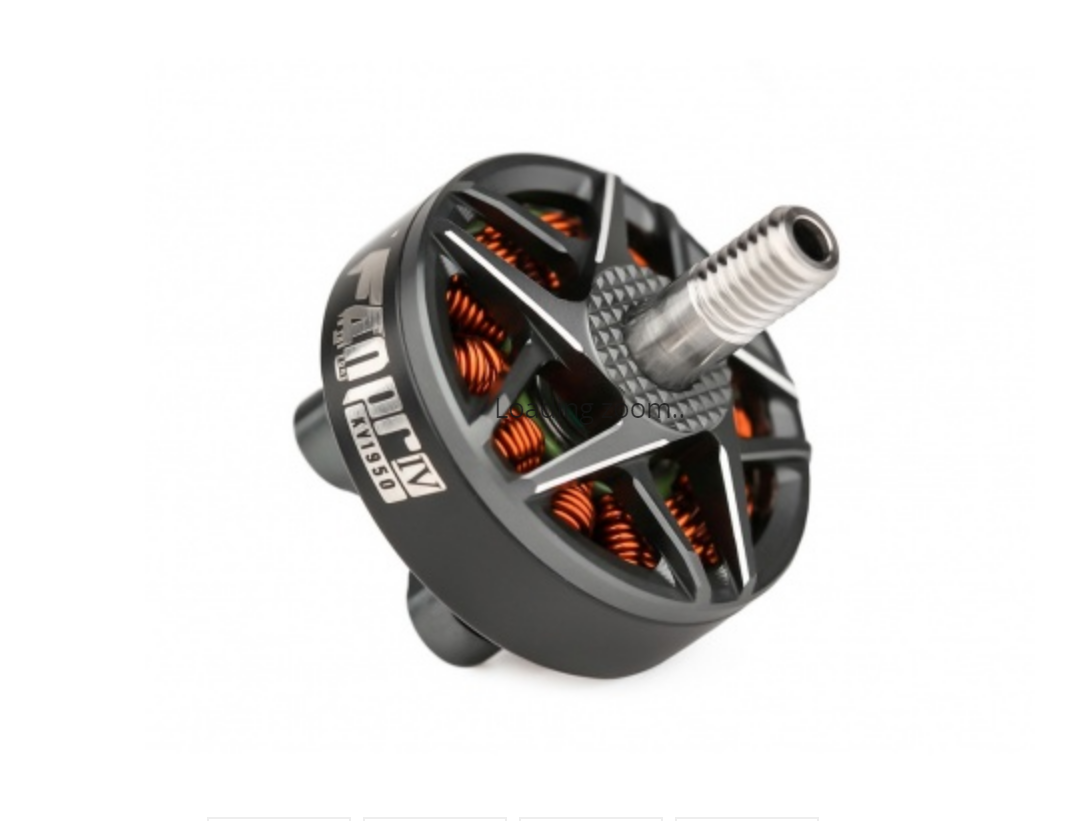
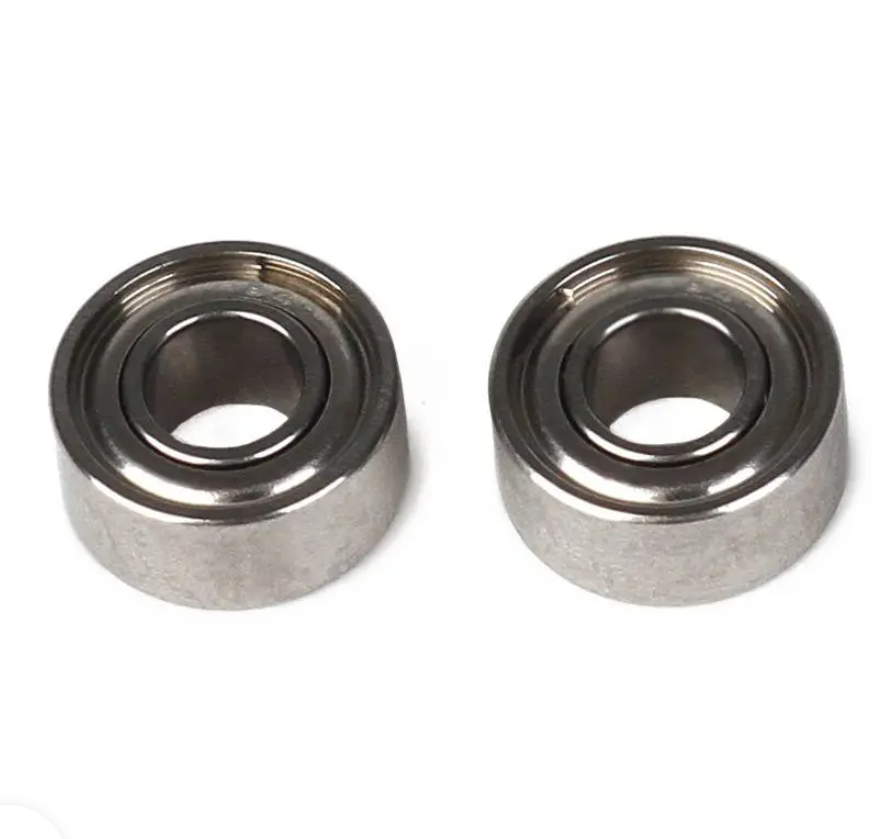
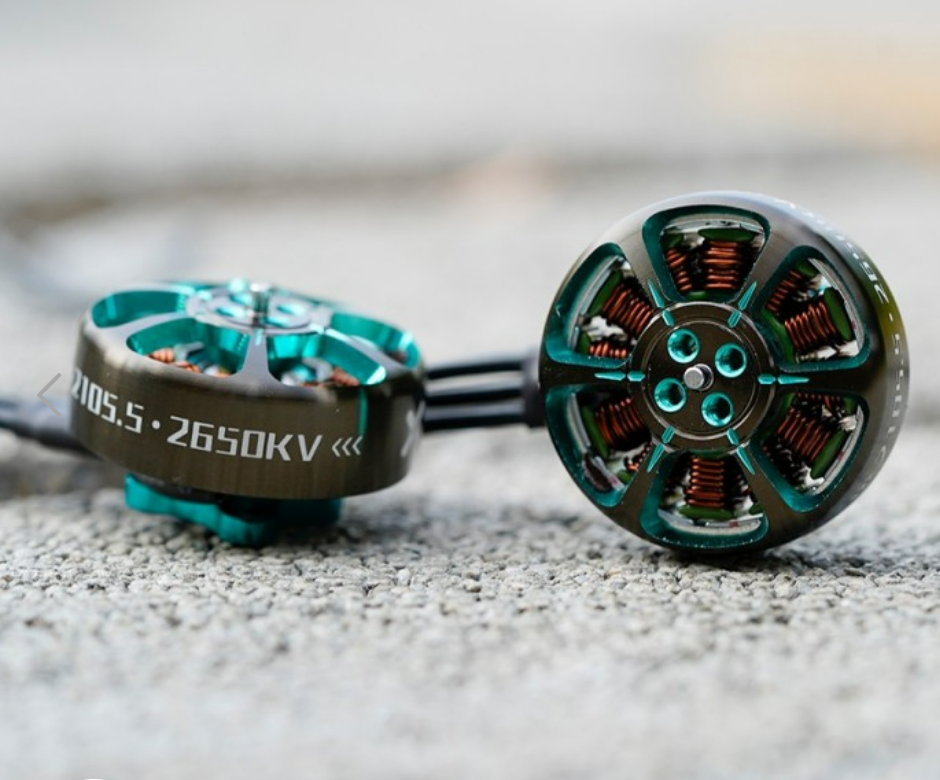
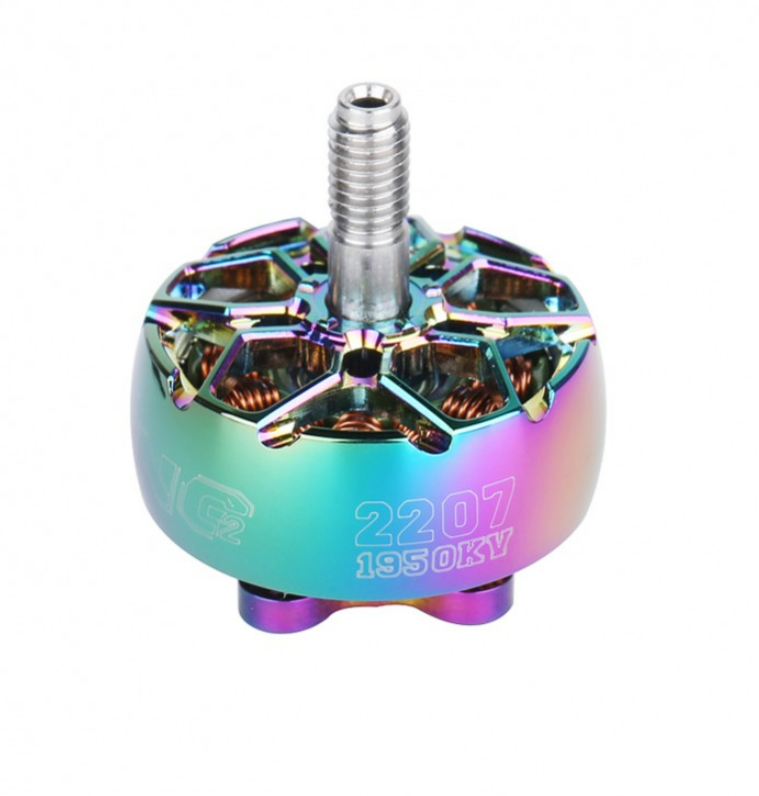
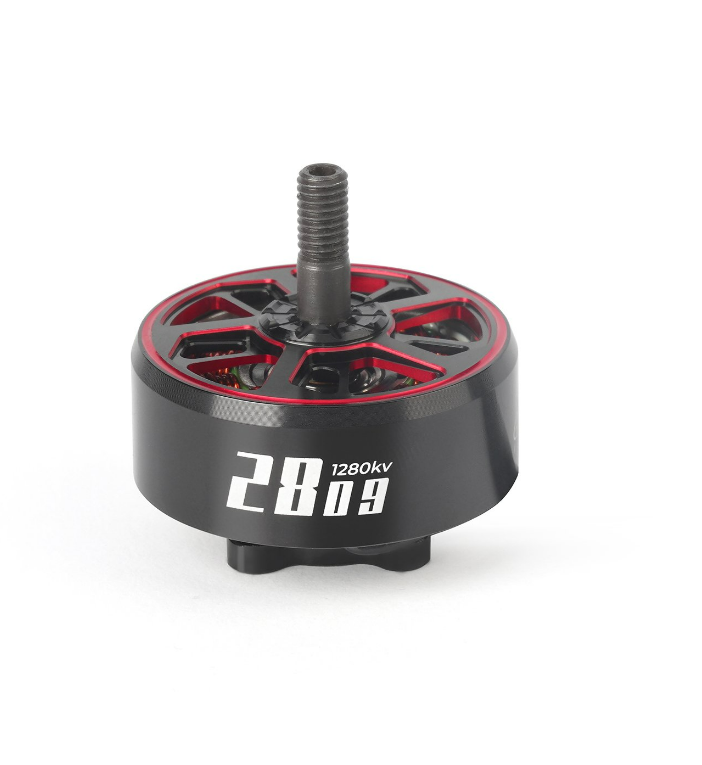
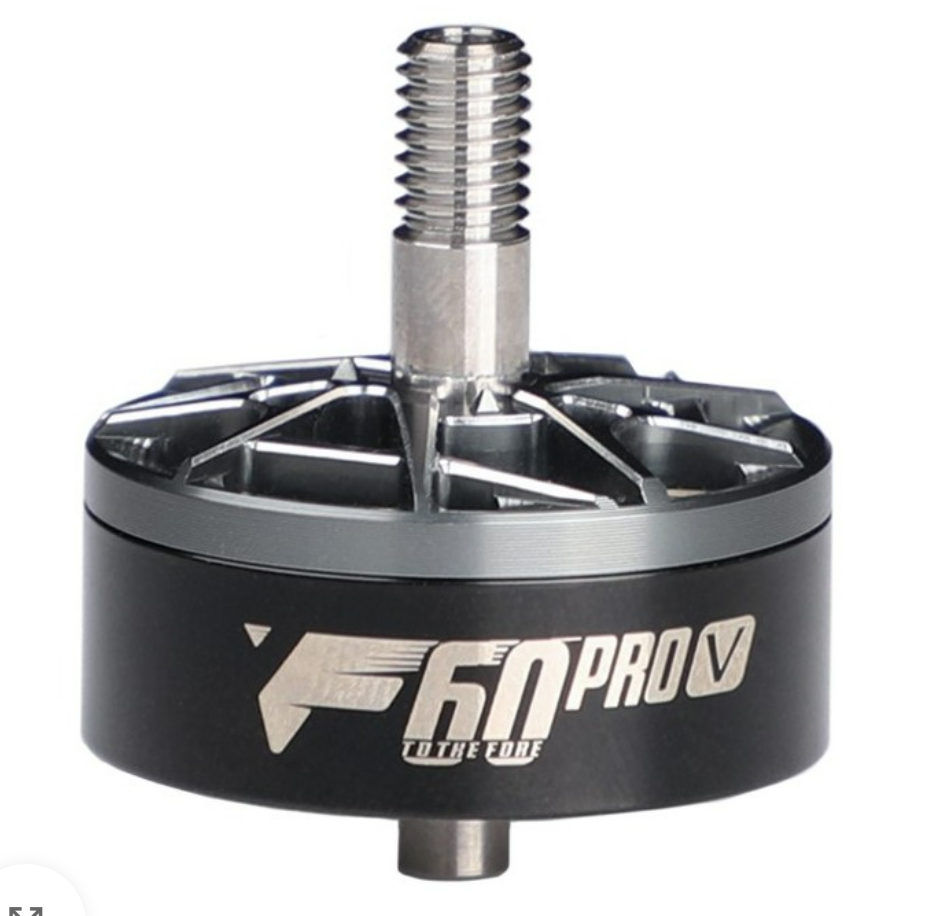
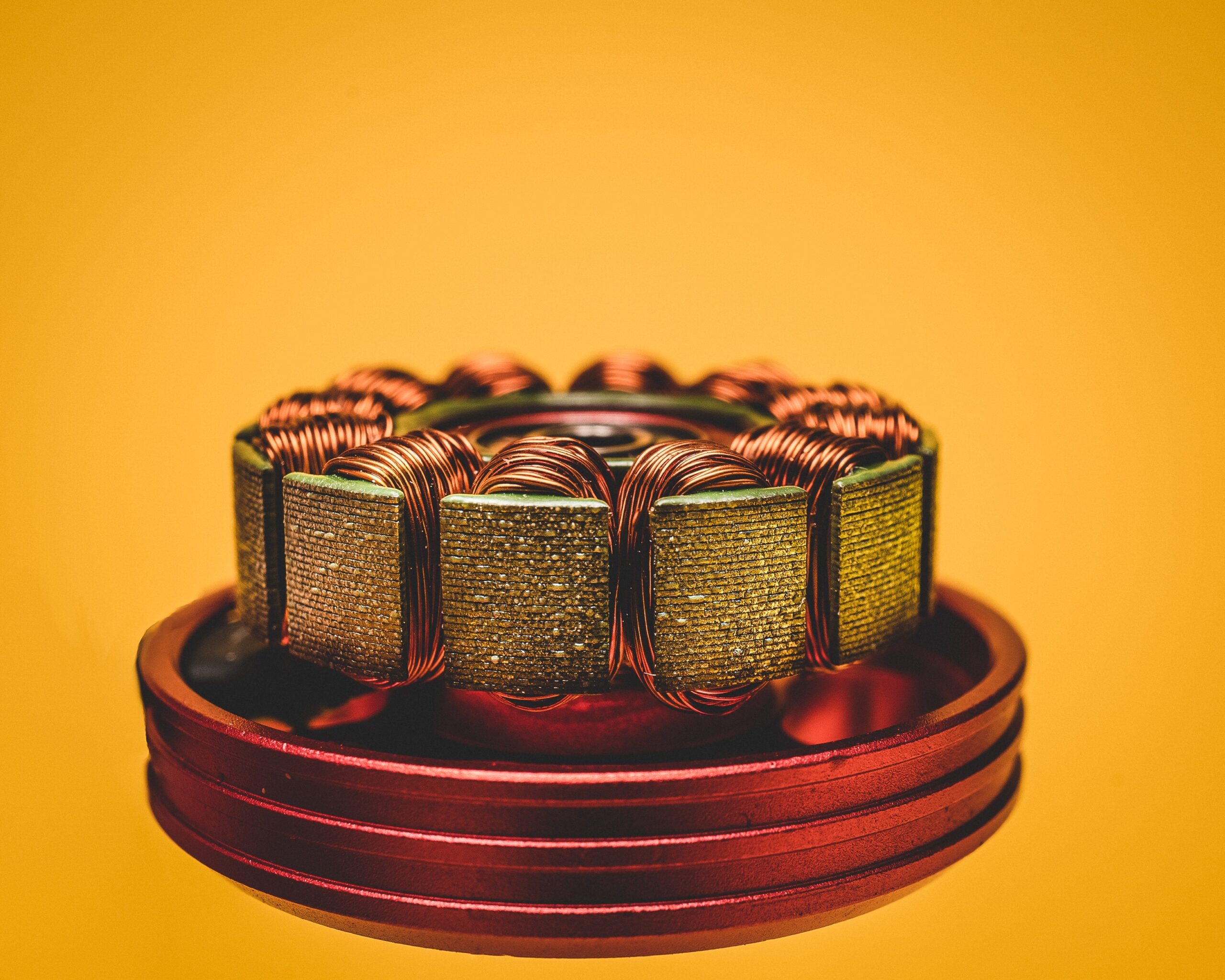
Electromechanical device designed to convert electrical energy into mechanical motion, thereby generating the necessary thrust to propel and navigate a drone through the air.
There are primarily two types of motors : brushless and brushed motors. Generally, the preference leans towards brushless motors for their enhanced durability and power.
A brushless DC electric motor, also known as an electronically commutated motor (ECM), operates on a direct current (DC) power supply. Instead of using a mechanical commutator with brushes, it employs an electronic controller to switch DC currents to the motor windings. This switching creates magnetic fields that rotate in space, guiding the movement of the permanent magnet rotor.
In contrast to brushed motors, where brushes and a commutator reverse the current flow in windings, brushless motors offer several advantages. They have a longer lifespan due to the absence of brushes that can wear down. Additionally, brushless motors are more powerful for their size, making them ideal for professional drones that prioritize reliability and power.
Working principle :
BLDC motor works on the principle similar to that of a Brushed DC motor. The Lorentz force law which states that whenever a current carrying conductor placed in a magnetic field it experiences a force. As a consequence of reaction force, the magnet will experience an equal and opposite force. In the BLDC motor, the current carrying conductor is stationary part and the permanent magnet is moving part.
The primary components of a motor are its internal stator and its outer bell. The stator is the circular array of stationary electromagnets. Each of the motor’s three wires supplies current to one-third of the electromagnets in its stator. The ESC’s job is to send current down each wire and excite the electromagnets in the right sequence and with the right timing. Permanent magnets line the inside of the motor bell, which spins the propeller affixed to the motor’s shaft. The two essential specifications for every motor are its size and KV.
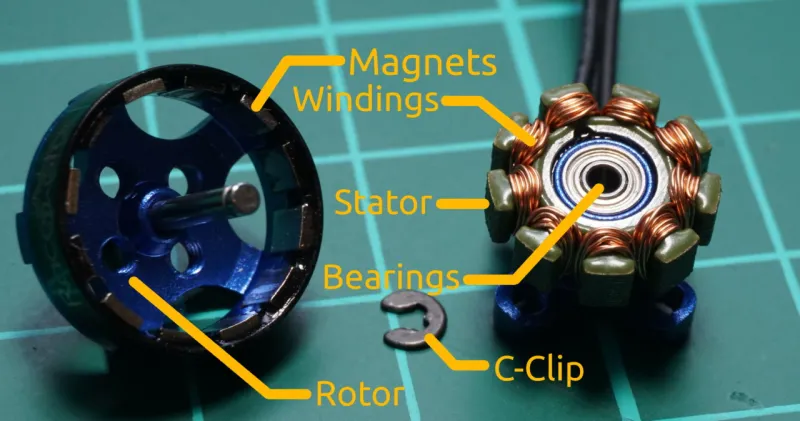
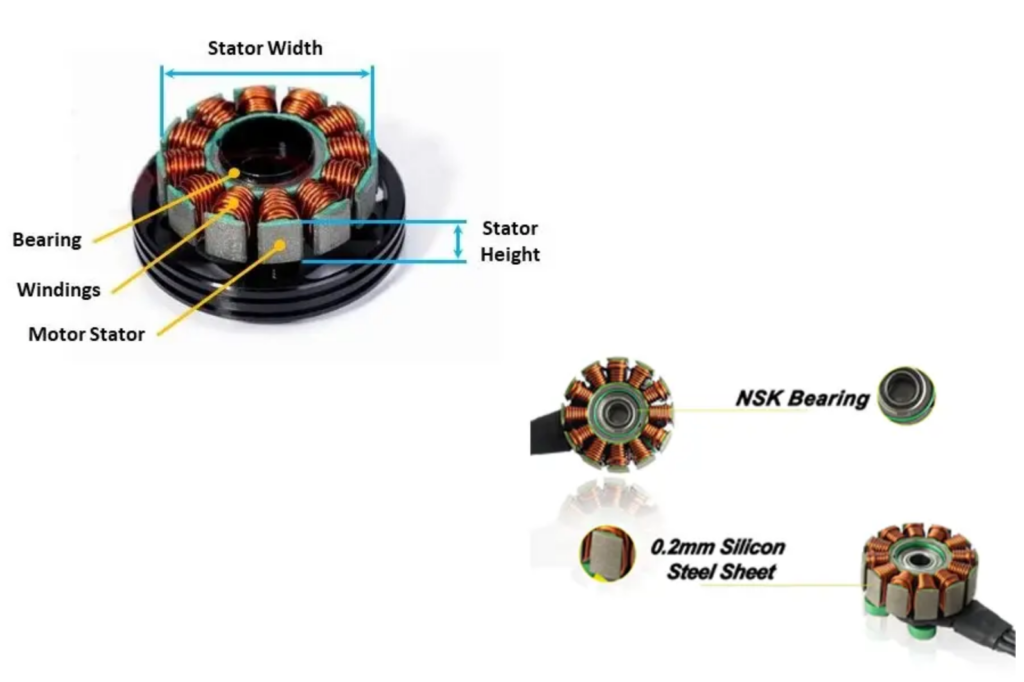
Motor Size (Stator Volume):
The motor size, or more accurately the dimensions of its stator, is represented by a four-digit number. The first two digits indicate the stator’s width/diameter in millimeters, and the last two digits tell us its height.
For example, a motor size of “2306” means the stator is 23mm wide and 6mm tall.
When the stator size of a motor increases, it generates more torque. In simple terms, “torque” is the twisting force that makes something rotate. For drones, motor torque indicates how quickly the propellers can spool up to a new RPM, affecting how responsive the quad feels in the air. Larger, torquey motors can quickly accelerate their attached props, making the drone feel agile and stable. However, the drawback is that these motors are heavier, draw more current, and increase the drone’s “moment of inertia,” requiring more effort to move.
K V :
KV is often mistaken for “kilovolt,” but it actually stands for “velocity constant.” KV tells us how fast a motor will spin with a specific voltage applied to its stator. It’s influenced by factors like the thickness and winding of the stator’s copper wires.
Motor KV × Voltage = Revolutions per minute
For example, if we connect a 2500KV motor to a fully charged 4S battery with 16.8V, the motor would theoretically spin at 42,000 RPM.
2500 kv ×(4×4.2) v = 42,000 RPM
A 1900KV motor connected to a fully charged 6S battery with 25.2V would also theoretically spin at 47,880 RPM.
1900 kv ×(6×4.2) v = 47,880 RPM
However, this is without any load, like a propeller, which would reduce the actual RPM and efficiency due to added weight and air drag. There’s an inverse relationship between motor KV and voltage, explaining why different-sized drones use motors with specific KV ranges.